Özyeğin University, Çekmeköy Campus Nişantepe District, Orman Street, 34794 Çekmeköy - İSTANBUL
Phone : +90 (216) 564 90 00
Fax : +90 (216) 564 99 99
E-mail: info@ozyegin.edu.tr
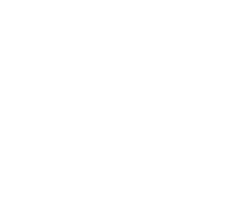
Dissertation Defense - Ozan Ekin Nural (PHDME)
Ozan Ekin Nural – Ph.D. Mechanical Engineering
Assoc. Prof. Özgür Ertunç – Advisor
Date: 29.12.2022
Time: 14.00
Location: AB3 236
DEVELOPING A METHODOLOGY FOR THE DESIGN AND
OPTIMIZATION OF THE PRESSURE-SWIRL ATOMIZERS
Assoc. Prof. Özgür Ertunç Özyeğin University
Prof. Mustafa Pınar Mengüç Özyeğin University
Assoc. Prof. Ayşe Gül Güngör Istanbul Technical University
Prof. Oğuz Uzol Middle East Technical University
Asst. Prof. Altuğ Melik Başol Özyeğin University
Abstract:
Atomization is the process of disintegration of bulk liquid into smaller droplets and has been an almost century-long research topic of fluid dynamics. Devices used for atomization are called atomizers and many different types of atomizers using different strategies to achieve atomization have been developed. Pressure-swirl atomizer is one of the most widely used types of atomizer due to its simplicity and ability to achieve a wide range of droplet sizes and coverage area. Even though the geometry of the pressure-swirl atomizer is simple, its internal flow field includes complex phenomena such as turbulence, liquid/gas interface, recirculation zones, and instabilities. Modeling the performance of pressure-swirl atomizer have been challenged by many researchers and different models were developed. Out of these models, 2D and 3D numerical simulations were proposed to be the most accurate ones, even though the accuracy of 2D simulations was questioned by many researchers. Other models, 1D models, and semi-empirical correlations also exist in the literature yet the accuracy of the latter is reported to be low. Models that could be used for the optimization of pressure-swirl atomizers, where it will be used to perform thousands of calculations while having low error values are lacking in the literature. Even though numerical modeling can result in accurate predictions, computation time prevents it to be used in optimization calculations. This study presents the developed models that could be used for such calculations and present their accuracy in comparison with conducted experiments and simulations. In this study first, inlet modeling of the 2D simulations is inspected. It was shown that the accuracy of the 2D simulations can be improved drastically by adjusting the inlet velocity components to include the effect of flow deformation that occurs due to tangential ports. It is shown that a model developed in an earlier study can be used to describe this deformation and calculate the inlet velocity components. Later, existing semi-empirical models in the literature along with the experimental data are presented and inspected. Overall 1,777 experimental data points, obtained from 34 different studies, are provided and cataloged. It is seen that, when the accuracy of semi-empirical correlations are evaluated in a global range, rather than in the range that they are developed at, error values increase significantly. A new set of semi-empirical correlations that are globally more accurate are obtained using experimental data. However, even with the developed correlations error values in the calculation of pressure difference and droplet sizes are still higher than 50 %. Due to the lack of the desired level of accuracy in the semi-empirical modeling, the boundary layer modeling approach is adopted for the description of the internal flow field of the pressure-swirl atomizer. Two different models, one for the straight sections (swirl chamber and orifice) and another for the convergent or divergent sections (convergent section or trumpet) are obtained. Evaluation of the model for the straight section is done with the comparison of the experimental data of open-end pressure swirl atomizers. Comparison of convergent or divergent section model is done with the 3D simulation of the unique atomizer geometry that is developed in the framework of this dissertation. Finally, accuracy of the combined model is evaluated with the experimental data of close-end pressure-swirl atomizers. Large number of 3D full geometry simulations are conducted to reason the coupling of internal flow dynamics with the uniformity of the pressure-swirl atomizer spray. These simulations are done with atomizer geometry having a unique shape and later three of the geometries are selected to be manufactured. Of the selected geometries two have uniform sprays while the third one has a non-uniform spray. Due to the unique shape of the inlets, these atomizers are manufactured with the method called Laser Lithography and the manufacturing tolerance of the geometries were less than 1 μm. Experiments of the atomizers are done with Laser Induced Fluorescence method at radial plane and obtained results showed having a non-uniform internal flow results in a spray where a cluster of droplets with large diameters exist. A semi-empirical model for the description of the non-uniformity is obtained and comparison with the existing model and experimental data in the literature is done. The spray of the pressure-swirl atomizer takes different shapes as the pressure and flow rate through the atomizer is increased and the final form of the spray is called fully- developed spray. The development of the spray of pressure-swirl atomizers is also modeled in this study. For this purpose, both experiments conducted in the framework of this study and experimental data obtained from the literature is used. A model that is based on the bulk Reynolds and Weber numbers is obtained using the gradient-descent method and comparisons with the existing correlations in the literature is done. Droplet diameter modeling is done by utilizing the model called Linear Instability Sheet Atomization (LISA) which is often used by commercial CFD codes. Analysis of this model is done by examining the equations and eight different correlations, differing in the simplifications, are obtained. Evaluation of these correlations are done by making comparisons with the experimental data of this study, which is obtained by the Shadowgraphy method. All of the droplet diameter experiments are conducted in the primary break-up region of the atomization. Comparisons have shown that, when the break-up length of the atomizer can be modeled accurately, LISA model can be used for the estimation of the representative droplet diameter. For the description of the droplet diameter distribution, a new model is obtained for the calculation of the spreading parameter. This parameter is often taken as constant in the commercial CFD codes yet it was shown that it has a significant effect on the obtained distributions. A comparison of the obtained model with the model of commercial CFD codes is also presented. Finally, the combination of the obtained models and their order of use for performing an optimization study is presented. It was also presented that obtained model can able to perform the calculation of single geometry in 20.0 seconds with a single core, whereas 2D and 3D simulations require 208 core-hour and 2,880 core-hour, respectively. It can be seen that the developed model is 37,440 times faster than 2D simulations and 518,440 times faster than 3D simulations.
Bio:
Ozan Ekin Nural received his BS degree from the mechanical engineering department of Istanbul Technical University, Turkey. He started working as a Ph.D. student under the supervision of Dr.-Ing Ozgur Ertunc in 2015 at the department of mechanical engineering at Ozyegin University. He is currently conducting studies on the modeling of the internal flow field of the pressure swirl atomizer and the resultant spray. His research interests include multi-phase flows, swirling flows, boundary layer modeling, and optimization.