Özyeğin Üniversitesi, Çekmeköy Kampüsü Nişantepe Mahallesi Orman Sokak 34794 Çekmeköy İstanbul
Telefon : +90 (216) 564 90 00
Fax : +90 (216) 564 99 99
info@ozyegin.edu.tr
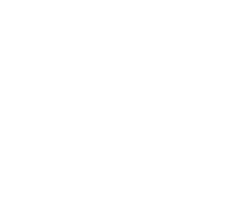
Thesis Defense - Gönenç Can Altun (MSME)
Gönenç Can Altun – M.Sc. Mechanical Engineering
Asst. Prof. Altuğ Belik Başol– Advisor
Date: 10.06.2021
Time: 18:00 – 19:00
Location: This meeting will be held ONLINE. Please send an e-mail to gizem.bakir@ozyegin.edu.tr in order to participate in this defense.
Numerical Investigation of the Radiant Heating Performance of a Continuous Annealing Furnace
Thesis Committee:
Asst. Prof. Altuğ Belik Başol, Özyeğin University
Prof. Dr. Pınar M. Mengüç, Özyeğin University
Prof. Dr. Tuba Okutucu Özyurt, İstanbul Technical University
Abstract:
Annealing as a type of heat treatment process is widely used in the glass manufacturing industry. It is the last stage of the manufacturing process and has a highly dominant effect on the quality of the glass. Especially in large volume glass manufacturing the annealing process is carried out in a continuous type annealing furnace. In those furnace the different stages of the annealing process are accomplished in the different zones of the same furnace. The main purpose of the heating zone of the furnace is to increase the temperature of the glass back to the annealing temperature. Due to the temperature levels reaching to 923 K inside the furnace, radiation heat transfer has a dominant effect in this zone of the furnace. Due to the mostly nonparticipating nature of the furnace atmosphere, the radiation heat transfer is governed by the view factors between the glass and the furnace walls. At the wavelength range of the radiation emitted from the furnace walls, the glass can be modelled as opaque. Since the view factor between the glass and the furnace walls depend on the distance between the glass rows inside the furnace, the layout of the glassware could have a considerable effect on the heating effectiveness of the furnace. In this numerical study, a combined conduction–radiation solver was developed to investigate the heating characteristics of moving bottles inside the radiant heating section of a continuous annealing furnace. The solver was designed as a hybrid solver running the conduction and the radiation calculations on the CPU and on the GPU (graphic processing unit) respectively. The radiation transfer between the opaque surfaces has been calculated with the Backward Monte Carlo Ray Tracing method. Running the method on the GPU, the computational cost of the radiation model has been massively reduced. Overall, 91% of the total computational time is spent by the radiation calculations and only 9% was taken by the heat conduction calculations. Moreover, two numerical methods regarding the integration of the radiation model with the heat conduction solver were developed. It was found that for the same level of accuracy the 2nd order accurate method enables to increase the time step in the transient calculations by a factor of two with respect to the 1st order accurate implementation. The considered furnace model consists of 29 bottle rows along the length of the furnace and with 15 bottles in each row. The initial temperature of the bottles was taken considering the molding stage of the manufacturing line. The computational cost of the problem was reduced by considering on the 7 rows of bottles in the computational domain. The developed algorithm enables to simulate the heat transfer across all the bottle rows using only a fraction of the entire row inside the furnace. Finally, a parametric study on the effect of the spacings between the bottle rows have been conducted. In this regard, the spacing between the bottles rows and the conveyor speed have been altered in a way that the throughput of the furnace, the number bottles processes per unit time, is kept constant. The study shows that there is an optimum value for the spacing between the bottle rows. For the considered bottle form, this optimum row spacing value is found to be 35% of the bottle diameter.
Bio:
Gönenç Can Altun was born in Ankara, Turkey on May 25, 1993. He received a Bachelor of Science degree in Mechanical Engineering from Gazi University. One year break after graduation he started to pursue academic studies supervised by Asst. Prof. Altuğ Melik Başol in Mechanical Engineering department of Özyeğin University.